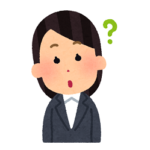
FMEAについて、目的や実践方法など、もう少し詳しく教えてください。
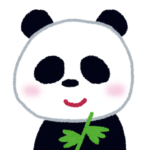
FMEAを導入する際には、あらゆる変化によって起こると想定される不具合を検討します。例えば、設備や人、方法や環境が変われば、想定する不具合も変わります。
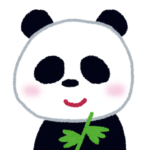
不具合の原因を「故障モード」・「故障モードの影響」を加味してトラブルを予防するのがFMEAの考え方です。
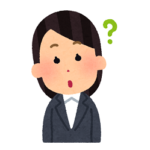
「故障モード」とは何ですか。「故障モード」と「故障」との違いは何ですか。
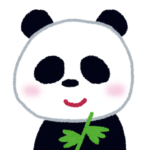
「故障モード (Failure Mode)」とは「故障の様子」、「故障 (Failure)」とは「目的の機能が損なわれた状態」を意味します。
例えば:
- 「故障モード (Failure Mode)」: モーターを構成する部品の断線 → 「故障 (Failure)」: モータが停止しない
- 「故障モード (Failure Mode)」: タイヤがパンクする → 「故障 (Failure)」 : 車が止まる
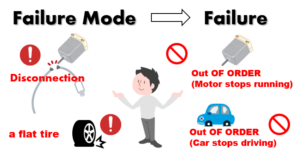
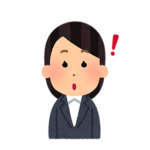
なるほど。
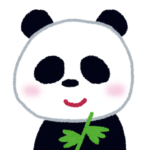
FMEAには大きく分けて、Design-FMEAとProcess-FMEAの2つのFMEAが存在します。
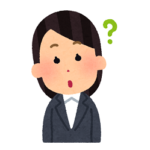
どう違いますか。
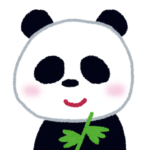
- Design-FMEA (D-FMEA) :製品設計に関するFMEA
- Process-FMEA (P-FMEA) :製品の製造工程に関するFMEA
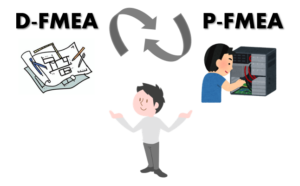
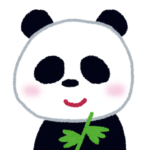
1つの製品を作る場合でも、設計観点だけでなく生産観点からの不具合の想定も必要で、よってD-FMEAとP-FMEAを繋げることが大切です。
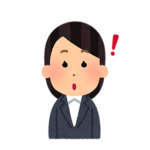
なるほど。FMEAは、信頼性の高い(=故障しにくい)製品や工程を設計する目的で実施するものなのですね。
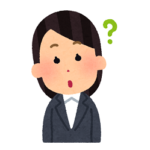
では、具体的にはどうやってFMEAを実践していくのでしょうか。
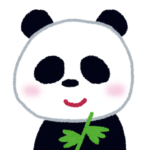
FMEAでは、重要度や発生率、検出度をもとに、リスク(RPN)を数値化することで、リスクの優先度を明確化します。RPNは『Risk Priority Number』の略語で、リスク優先度です。
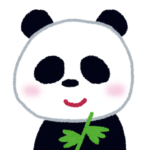
① 故障のモード(想定させる不具合事象)を入力する
② その故障が製品や顧客に与える具体的な内容を入力する
③ その影響が与える重要度を10段階で入力する
④ 故障が発生する可能性のある原因を入力する
⑤ 故障が発生する発生率を10段階で入力する
⑥ 故障を検出できる可能性がある方法(検査方法)を入力する
⑦ 検査方法から検出率を10段階で入力する
⑧ 重要度③×発生率⑤×検出度⑦ でリスク(RPN)を計算する
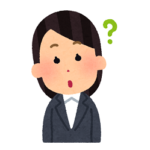
これらのステップでリスク(RPN)を数値化できるのですね。
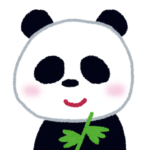
続いて、以下を実行ながら、リスクを下げていきます。
⑨ リスクが高い項目の場合、リスクを下げる改善策の内容を入力する
⑩ 改善後のRPNを計算する
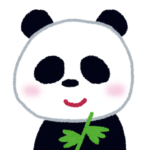
上記のステップのなかでも、①②は特に大切です。考えられるリスクをあげればあげる程、良いFMEAになり、完成度があがるといわれています。
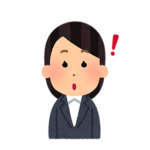
FMEAにおける対策(RPNを下げる)手段は、『発生度を下げる』若しくは『検出度を下げる』ことなんですね。
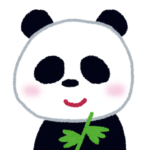
その通りです。
IATF16949:2016 10.2.3 問題解決でも、不適合が発生した際の是正処置について『適切な文書化した情報のレビュー及び必要に応じた更新』の要求事項が書かれています。
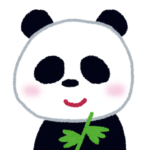
FMEAは次モデルを開発するときに、前モデルのFMEAを参考に書き足していくので、次モデルに対する不具合の再発防止としても役立ちます。
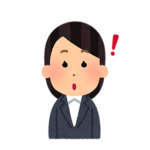
なるほど。
FMEAは、作るのは時間もかかり大変ですが、作ってしまえば次モデルでも活用できる資産になるんですね。
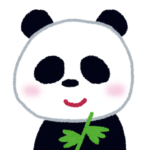
NSSでは、システマティックな故障分析を実現する品質管理(FMEA/故障モード影響解析)ツール「APIS IQ」を販売しております。
「APIS IQ」について、詳しくはコチラから。